falcosms
New member
Hello all..
i´m working in a smps flyback 138W DCM
input: 80 - 250 Vac, output 13,8V x 10 A.
the schematic is this: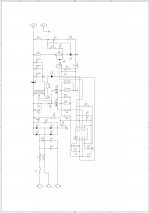
it´s working, but when i apply load (about 4 A) the leakage voltage across the mosfet is very high... look: View attachment osc.bmp.
the transformer is 42/15 core, prim 11 + 11 turns, secondary 3 turns, inductance primary of 150 uH. the assembly of primary and secondary are good.
i´m reading about this issue at web, but i don´t found nothing to solve this.
i think the problem is in the transformer, but i can´t solve.
sincerely
marcelo
i´m working in a smps flyback 138W DCM
input: 80 - 250 Vac, output 13,8V x 10 A.
the schematic is this:
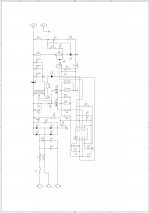
it´s working, but when i apply load (about 4 A) the leakage voltage across the mosfet is very high... look: View attachment osc.bmp.
the transformer is 42/15 core, prim 11 + 11 turns, secondary 3 turns, inductance primary of 150 uH. the assembly of primary and secondary are good.
i´m reading about this issue at web, but i don´t found nothing to solve this.
i think the problem is in the transformer, but i can´t solve.
sincerely
marcelo