crazifunguy
New member
Hello SMPS Community
I am working on a SMPS that I would like to use for some amps I want to build. I have some schematics for a CCM PFC and a DC-DC converter. The design could meet class D and 80+ specs according simulation tests. I do however have some questions. I am well rounded in electronics but I need some design help. Here are my specs so far.
PFC Input Voltage
85V - 265V AC 50/60HZ
PFC Output Voltage
400V DC
~4A
DC-DC Converter Output Voltage
+70V 10A -70V 10A
Total Power ~1400W
Topology
CCM PFC with Half Bridge DC-DC
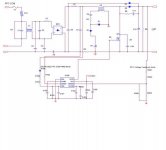
Using PowerEsim
L1 L2 & L3 are shown using 8 AWG wire. This seems too large. How do I calculate a proper wire size for these chokes and inductors??
I am working on a SMPS that I would like to use for some amps I want to build. I have some schematics for a CCM PFC and a DC-DC converter. The design could meet class D and 80+ specs according simulation tests. I do however have some questions. I am well rounded in electronics but I need some design help. Here are my specs so far.
PFC Input Voltage
85V - 265V AC 50/60HZ
PFC Output Voltage
400V DC
~4A
DC-DC Converter Output Voltage
+70V 10A -70V 10A
Total Power ~1400W
Topology
CCM PFC with Half Bridge DC-DC
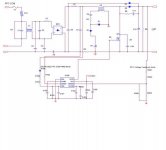
Using PowerEsim
L1 L2 & L3 are shown using 8 AWG wire. This seems too large. How do I calculate a proper wire size for these chokes and inductors??
Last edited: